Saudi-Dutch JV seeks contractors for metals reclamation project
5 July 2024
Saudi Arabia’s Advanced Circular Materials Company (ACMC), a joint venture between The Netherlands-based Shell & AMG Recycling BV (SARBV) and local firm United Company for Industry (UCI), has solicited interest from contractors to build a metals reclamation facility in the kingdom.
ACMC has approached local and international contractors to submit prequalification documents for the engineering, procurement and construction (EPC) works on the planned project by 21 July.
Front-end engineering and design work on the project is in its “conclusion phase”, SARBV, the lead partner in the project, said in a statement. The facility is scheduled to enter commercial operations by the end of 2026.
SARBV first announced its intention to build a metal reclamation and catalyst manufacturing facility in Saudi Arabia in November 2019. The kingdom’s Ministry of Investment, then known as the Saudi Arabian General Investment Authority (Sagia), supported the project.
In July 2022, SARBV and UCI signed an agreement to formalise their joint venture and build the proposed facility in PlasChem Park in Jubail Industrial City, in Saudi Arabia’s Eastern Province.
The project has received support from Saudi Aramco’s Namaat industrial investment programme. Aramco, at the time, also signed an agreement with the joint venture to offtake vanadium-bearing gasification ash from the Jazan refining complex, to be produced as part of the first phase of the project.
Metals recycling facility
ACMC has divided the project in four phases. Phase 1 will process gasification ash generated by the Jazan refining complex to produce battery-grade vanadium oxide and vanadium electrolyte for vanadium redox flow batteries. AMG will provide the licensed technology required for the production process.
At nominal capacity, the first phase of the project will process 7,000 metric tonnes year of vanadium concentrate. ACMC has allocated a budget of $200m approximately for this phase.
Phase 2 would expand the facility to process spent catalyst from heavy oil upgrading facilities to produce ferrovanadium for the steel industry and/or additional battery grade vanadium oxide.
Phase 3 involves the installation of a manufacturing facility for residue upgrading catalysts.
In the fourth phase, a vanadium electrolyte production plant is to be developed.
The developers expect total carbon dioxide emissions reduction of 3.6 million metric tonnes a year when the four phases of the project are commissioned.
Photo credit: SARBV
Exclusive from Meed
-
Soudah Peaks outlines project construction plans
3 July 2025
-
Read the July 2025 MEED Business Review
3 July 2025
-
Algeria plans to expand fertiliser plant
3 July 2025
-
-
All of this is only 1% of what MEED.com has to offer
Subscribe now and unlock all the 153,671 articles on MEED.com
- All the latest news, data, and market intelligence across MENA at your fingerprints
- First-hand updates and inside information on projects, clients and competitors that matter to you
- 20 years' archive of information, data, and news for you to access at your convenience
- Strategize to succeed and minimise risks with timely analysis of current and future market trends
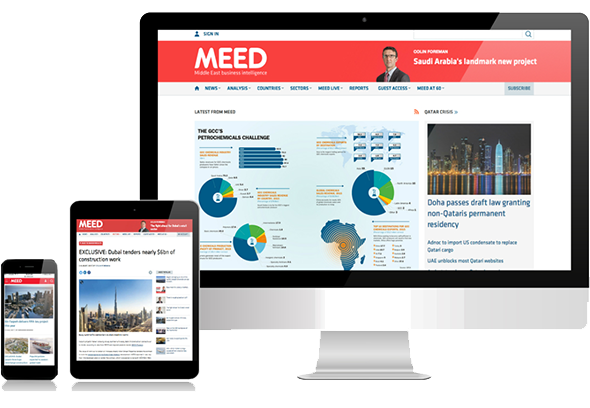
Related Articles
-
Soudah Peaks outlines project construction plans
3 July 2025
Register for MEED’s 14-day trial access
Saudi Arabia’s Soudah Development Company (SDC) has outlined plans to tender the upcoming construction work at its Soudah Peaks project in the Aseer region.
While presenting a webinar hosted by MEED on 3 July, Daniel McBrearty, chief development officer at Soudah Peaks, said: “We have several packages ready to be floated to the market by the end of this year.
“The most immediate of these is the development of site-wide infrastructure required for the project.
“The high-voltage electrical infrastructure catering to Soudah Peaks will be tendered by Saudi Electricity Company.”
This package includes one bulk supply point with a capacity of 380kV /132kV, two primary substations and 142 distribution substations.
The development will also require 15 water storage tanks and pump stations. The tanks will have a storage capacity of 93,150 cubic metres to cater to an expected demand of about 10,984 cubic metres a day (cm/d).
A total of 14 sewage treatment plants are also planned, with a total capacity of 10,690 cm/d. The development will require 52 sewage lifting stations.
The infrastructure package will also cover 24 mobile telecommunications or GSM (global system for mobile communications) towers and the relocation of eight existing GSM towers, as well as a package for the drainage culvert.
SDC began the project procurement process in May when it floated a tender to bid for a contract to develop an employee housing package that will be developed using a design, build, finance, operate and maintain model.
The tendering timelines are:
- WP1 Zone 1 Tahlal Town Centre: May 2026
- WP2 Zone 1 Tahlal Ridge: August 2026
- WP3 Zone 1,2,3,6 Tahlal residential, Sahab, Sabrah and Redrock: June 2026
- WP4 Zone 5 Rijal: April 2026
- WP5 Site-wide infrastructure: December 2025
- General Contractor: Floated in May 2025
- Contractor Workforce Housing: Floated in March 2025
Six development zones
“The overall masterplan covers an area of more than 635 square kilometres and consists of six development zones: Tahlal, Sahab, Sabrah, Jareen, Rijal and Red Rock,” McBrearty said.
Tahlal offers a mix of residential, hospitality, heritage and retail facilities, along with an 18-hole golf course and the Watan Am-Soudah heritage village.
Sahab will be an international destination for adventure sports and recreation. It will provide views across the valley and within the rolling plateau landscape.
Sabrah provides a luxury residential destination supported by high-end hospitality. The development is integrated within the contours and is provided within a natural open space context.
Rijal will be a hospitality destination with integrated views through to the Rijal Cultural Village. The development is built around the existing development, which gives the village its character.
The Red Rock zone will offer luxury hospitality, with mansions and glamping camps set within the national park.
Jareen offers a genuine approach to connecting with nature through authentic experiences within the agricultural landscape.
Jareen will be developed as part of the third phase, when the infrastructure and connectivity are fully established within the development.
Three phases
“The masterplan will be developed in three phases, and the first phase will include the development of five out of the development’s six zones,” McBrearty said.
The overall development will offer 2,810 hotel rooms, 1,337 residential units and 30 other attractions.
The first phase will include 940 hotel keys, 391 residential units and 1,025 staff accommodation units.
The second phase will increase the total to 1,735 hotel rooms, 641 residential units and 2,150 staff accommodation units.
The final phase will have over 2,810 hotel rooms, 1,337 residential units and 3,022 staff accommodation units.
We have several packages ready to be floated to the market by the end of this year. The most immediate of these is the development of site-wide infrastructure required for the project
Daniel McBrearty, Soudah PeaksCompanies engaged
In March, SDC appointed US-based engineering firm Aecom as the lead design consultant for the Soudah Peaks development.
Aecom’s scope of work covers the design work for the first phase of the development.
Last year, SDC appointed another US-based engineering firm, Parsons Corporation, as the project management consultant for the development.
Parsons’ scope of work includes project management and site supervision services for the six development zones.
Project background
Soudah Peaks is a mountain tourism destination set 3,015 metres above sea level on the country’s highest peak in the Aseer region.
The project masterplan was formally launched in September 2023 by Saudi Arabia’s Crown Prince Mohammed Bin Salman Al-Saud.
Speaking at the launch, he said: “Soudah Peaks will be a significant addition to the tourism sector in Saudi Arabia and place the kingdom on the global tourism map while highlighting and celebrating the country’s rich culture and heritage.”
Launched in 2021, SDC is wholly owned by Saudi Arabia’s sovereign wealth vehicle, the Public Investment Fund.
An investment of SR11bn ($3bn) has been planned to develop tourism infrastructure and attractions in the Aseer region in the southwest of the kingdom.
SDC intends to partner with the local community and private sector to develop hospitality, residential, commercial and entertainment offerings that will attract more than 2 million visitors a year, creating 8,000 direct and indirect permanent jobs by 2030.
https://image.digitalinsightresearch.in/uploads/NewsArticle/14194455/main.jpg -
Read the July 2025 MEED Business Review
3 July 2025
Download / Subscribe / 14-day trial access The UAE’s investments in Turkiye, along with the contracts won by Turkish firms in the UAE, highlight the mutual opportunities available to both countries.
Turkiye is already the UAE’s fourth-largest non-oil trading partner, rising from seventh place in 2021. Last year, non-oil trade between the UAE and Turkiye grew by 11.5%, reaching $40.5bn.
With this momentum set to continue, MEED's latest issue takes an in-depth look at the growing trade relationship between the two countries.
In our 10-page opening Agenda section, MEED editor Colin Foreman speaks exclusively to the president of the investment and finance office of the Presidency of the Republic of Turkiye, Burak Daglioglu, about bilateral investment; and talks to Kalyon Holding CEO Mustafa Kocar about the construction firm’s new focus on the Middle East.
There are also interviews with DenizBank CEO Recep Bastug, on the strengthening financial links, and with the vice-president of sales at Turkish Airlines, Erol Senol, on the airline’s plans for further growth.
This month’s Levant market focus covers Jordan, Lebanon and Syria and finds all three countries working to recover from recent events beyond their control.
MEED's latest issue also includes a comprehensive GCC real estate report, covering all six markets in detail. While growth is continuing, the sector is showing signs of facing a more nuanced reality due to economic slowdown, regional tensions, oversupply risks and delivery constraints. Read more here.
We hope our valued subscribers enjoy the July 2025 issue of MEED Business Review.
Must-read sections in the July 2025 issue of MEED Business Review include:
> AGENDA:
> UAE-Turkiye trade gains momentum
> Building on UAE-Turkiye trade
> Turkiye's Kalyon goes global
> Strengthening UAE-Turkiye financial links
> Turkish Airlines plans further growth> CURRENT AFFAIRS:
> Middle East tensions could reduce gas investmentsINDUSTRY REPORT:
GCC real estate
> GCC real estate faces a more nuanced reality> PROJECTS: GCC projects market collapses
> INTERVIEW: Hassan Allam eyes role in Saudi Arabia’s transformation
> INTERVIEW: Aseer region seeks new investments for Saudi Arabia
> LEADERSHIP: Nuclear power makes a global comeback
> LEVANT MARKET REPORT:
> COMMENT: Levant states wrestle regional pressures
> ECONOMY: Jordan economy nears inflection point
> GAS: Jordan pushes ahead with gas plans
> POWER & WATER: Record-breaking year for Jordan’s water sector
> CONSTRUCTION: PPP schemes to drive Jordan construction
> DATABANK: Jordan’s economy holds pace, for now
> ECONOMY: Lebanon’s outlook remains fraught
> RECONSTRUCTION: Who will fund Syria’s $1tn rebuild?> MEED COMMENTS:
> Dubai's tall towers reach new heights
> Contractors return to Palm Jebel Ali
> Nuclear U-turn is an opportunity
> Adnoc pursues global gas ambition> GULF PROJECTS INDEX: Gulf projects index continues climb
> MAY 2025 CONTRACTS: Mena contract award activity remains subdued
> ECONOMIC DATA: Data drives regional projects
> OPINION: A farcical tragedy that no one can end
> BUSINESS OUTLOOK: Finance, oil and gas, construction, power and water contracts
To see previous issues of MEED Business Review, please click herehttps://image.digitalinsightresearch.in/uploads/NewsArticle/14193655/main.gif -
Algeria plans to expand fertiliser plant
3 July 2025
Algeria’s national oil and gas company Sonatrach is developing a project that will expand the country’s fertiliser plant located in Arzew, according to industry sources.
Sonatrach has not publicly said when it expects to issue the invitation to bid for the main contract for the project.
The original $2.4bn contract to develop the Arzew Fertiliser Complex was executed by a joint venture of South Korea’s Daewoo E&C and Japan’s Mitsubishi Corporation.
The joint venture won the contract in April 2008 and completed the facility in April 2013.
The fertiliser production complex was built in the Arzew industrial zone near Oran, on the Mediterranean coast.
It produces ammonia from natural gas, and almost all of the ammonia output is converted to urea for producing granular urea to be used as fertiliser.
The complex includes two ammonia production units, each with a capacity of 2,000 tonnes a day (t/d).
It also includes two urea production units, each with a capacity of 3,500 t/d, as well as granulation plants and supporting facilities.
Sonatrach is currently trying to boost Algeria’s capacity to produce fertilisers.
In December, a total of six companies were shortlisted as part of the tender process for another fertiliser project in Algeria’s Annaba region, according to information released by the Industrial Group for Fertilisers & Phytosanitary Products (Asmidal).
Asmidal is a wholly owned subsidiary of Sonatrach.
The scope of the contract being tendered included preparing a front-end engineering and design (feed) study for a project to create a fertilisers, food phosphates and derivatives complex.
The project is expected to be worth about $1bn.
https://image.digitalinsightresearch.in/uploads/NewsArticle/14192053/main.jpg -
Kuwait extends bid deadlines for projects worth $1.57bn
3 July 2025
State-owned upstream operator Kuwait Oil Company (KOC) has extended the bid deadlines for four strategic oil projects worth a total of $1.57bn.
The first contract, estimated to be worth KD292m ($951m), is focused on developing a separation facility in the NK SA/BA Area, close to Gathering Centre 23 (GC-23) and GC-24.
The scope of the contract also includes a new injection facility at GC-31 and effluent water injection networks in north Kuwait.
The project’s latest bid deadline has been set for 22 July.
The second contract is to develop the planned Mutriba remote boosting facility in northwest Kuwait.
It was originally tendered earlier this year with a bid submission deadline of 29 June. The deadline has now been extended to 27 July 2025.
The project has an estimated budget of about KD130m ($420m) and its scope includes:
- Development of the Mutriba oil field
- Installation of the degassing station
- Installation of manifolds
- Installation of condensate facilities
- Installation of wellhead separation units
- Installation of the pumping system
- Installation of wellhead facilities
- Installation of oil and gas treatment plants
- Installation of a natural gas liquid plant
- Installation of a water and gas injection plant
- Construction of associated utilities and facilities
The onshore Mutriba oil field is located in northwest Kuwait.
In October 2024, KOC announced that it was preparing to tender a project management contract for a scheme to develop the field.
At the time, it said four international companies had been invited to participate in the tender process. These were:
- Schlumberger (US)
- Halliburton (US)
- Baker Hughes (US)
- Weatherford International (US)
KOC also said that the list of qualified companies could be extended before the invitation to bid was issued.
The third project, estimated to be worth $100m, is for an effluent water injection network in north Kuwait.
Effluent water injection or water flooding is a secondary hydrocarbons recovery technique where produced water is injected into a well’s formation under high pressure and temperature conditions to recover more of the oil initially in place.
The bid deadline has been extended from 24 June to 22 July 2025.
The fourth project is estimated to be worth around $100m and is focused on the construction of a new injection network in north Kuwait that will service the Sabriyah/Bahra (SA/BA) area.
Its bid deadline has also been extended from 24 June to 22 July 2025.
Kuwait is in the middle of an upstream projects push, in line with its goal of producing 4 million barrels a day of oil by 2035.
https://image.digitalinsightresearch.in/uploads/NewsArticle/14192034/main.jpg -
Miral tenders Harry Potter attraction in Abu Dhabi
3 July 2025
Register for MEED’s 14-day trial access
Abu Dhabi’s Miral has started the procurement process for the contract to build the Harry Potter-themed expansion to the Warner Bros World Yas Island entertainment destination in Abu Dhabi.
According to sources close to the project, the tender for the estimated AED2bn-AED3bn ($545m-$816m) main construction works has been issued to contractors, with bids due in July.
The scope of the Warner Bros World phase two expansion includes adding 40,000 square metres (sq m) to the existing theme park. This will include a Harry Potter-themed zone with three new rides, retail, and food and beverage outlets.
The enabling works on the project have begun and are being undertaken by the local firm NSCC International. Another local firm, Emirates Electrical & Instrumentation Company, is undertaking the early works on the project.
Canadian engineering firm Ellisdon is the project consultant.
Responding to a request for a comment, Miral said relevant project updates would be shared in due course. “Miral does not comment on speculative and inaccurate information from unknown sources,” the developer said.
According to media reports, the Abu Dhabi project will be the world’s sixth Harry Potter-themed park. The others are in Florida and California in the US, Beijing in China, Osaka in Japan and Leavesden in the UK.
The Abu Dhabi project was first announced in November 2022.
Yas Waterworld
Miral has developed a series of theme parks and other entertainment-related attractions on Yas Island and has worked with several local and international contracting companies.
On 1 July, Miral opened the new 16,900 sq m expansion of its Yas Waterworld park to the public.
The expansion added 3.3 kilometres of slide sections to the park. The addition of 18 new rides and attractions, bringing the total number of rides to more than 60, is expected to grow visitor capacity by 20%.
The construction was carried out by the local contractor Alec.
Disney park
In May, The Walt Disney Company and Miral signed an agreement to build a Disney theme park resort on Yas Island.
Disney, which is based in the US, said it will be its seventh theme park resort. The others are in California and Florida in the US, Paris in France, Hong Kong and Shanghai in China and Tokyo in Japan.
In a statement, Disney highlighted that the UAE is located within a four-hour flight of one-third of the world’s population, making it a significant gateway for tourism. It is also home to the largest global airline hub in the world, with 120 million passengers travelling through Abu Dhabi and Dubai each year.
The Disney theme park resort in Abu Dhabi will include entertainment areas, themed accommodations, and dining and retail experiences.
Abu Dhabi hopes bigger is better with Disney theme park
In 2023, Miral opened SeaWorld Abu Dhabi, also on Yas Island. Alec was the contractor for the estimated $565m project.
In 2018, Miral opened the Warner Bros theme park on Yas Island. Belgium’s Besix was the contractor for the estimated $531m project.
Miral has developed a series of theme parks and other entertainment-related attractions on Yas Island
Other Miral projects have included the Etihad Arena and the indoor climbing and skydive centre Clymb. Bam of the Netherlands was the contractor for the Arena and Germany’s Zublin was the contractor for Clymb.
Yas Island was launched as a project in 2006 by local developer Aldar Properties. The original centrepiece attractions were the Yas Marina Circuit, which hosts Formula 1 motor racing’s annual Abu Dhabi Grand Prix, and the Ferrari World theme park.
https://image.digitalinsightresearch.in/uploads/NewsArticle/14186919/main.jpg