Gulf charts pathway to clean steel production
1 August 2024
Steel manufacturing accounts for 7%-9% of global carbon dioxide (CO2) emissions and is considered a hard-to-abate industry. With a forecast for strong growth in global steel production in the coming decades, changes need to be implemented to bring steelmaking in line with the UN Paris Climate Agreement goal of limiting global warming to 1.5 degrees Celsius.
The need for the international steel industry to slash CO2 and greenhouse gas emissions dominated the agenda at UN climate change summit Cop28 in Dubai last December, with about 35 companies and six industry associations, including the World Steel Association, endorsing the Industrial Transition Accelerator. The initiative aims to scale implementation and delivery of decarbonisation in the steel, aluminum, cement, transportation and energy sectors.
There are many levers for steel decarbonisation, including the electrification of heat generation, improving energy efficiency and increasing the utilisation of scrap steel. However, to reach net-zero, further steps are needed to address the emissions associated with coal’s role as a reducing agent in ironmaking. Breakthrough technologies that can accomplish this include hydrogen direct reduction to replace coal; carbon capture, utilisation and storage; and electrolysis-based, or green hydrogen-supported, production processes.
The Middle East and North Africa accounts for just 5% of global steel output. Despite this low market share, however, steelmakers in the region – particularly in the Gulf – have committed billions of dollars to investments in steel projects that could implement most proven clean technologies.
To reach net-zero, further steps are needed to address the emissions associated with coal’s role as a reducing agent in ironmaking
Saudi clean steel projects
Saudi Aramco, the kingdom’s sovereign wealth institution the Public Investment Fund (PIF) and Chinese steel manufacturing conglomerate Baoshan Iron & Steel Company (Baosteel) signed a joint venture agreement in May 2023 to establish an integrated steel plate manufacturing complex in Saudi Arabia’s Ras Al-Khair Industrial City.
The facility is expected to have a production capacity of up to 1.5 million tonnes a year (t/y). It will mainly cater to industrial sectors such as pipelines, shipbuilding, rig manufacturing, offshore platform fabrication and tank and pressure vessel manufacturing, as well as the construction, renewables and marine sectors.
The plant will be equipped with a natural gas-based direct reduced iron (DRI) furnace and an electric arc furnace to reduce CO2 emissions from the steelmaking process by up to 60% compared to a traditional blast furnace. The DRI plant will be compatible with hydrogen without major equipment modifications, potentially reducing CO2 emissions by up to 90% in the future, Aramco says.
The partners have invited contractors to submit engineering, procurement, installation and construction proposals for the project, which are due by 30 July.
Separately, Indian industrial conglomerate Essar Group is advancing its planned $4bn Green Steel Arabia project, which will also be located in Ras Al-Khair. Essar’s integrated steel complex will have a production capacity of 4 million t/y, and a cold rolling capacity of 1 million t/y, along with galvanising and tin plate lines. The complex will also have two DRI plants, each with a production capacity of 2.5 million t/y.
In September 2023, Essar signed a memorandum of understanding (MoU) with Jeddah-based Desert Technologies to develop solar energy solutions to power its Green Steel Arabia project. Under the agreement, Essar and Desert Technologies will look to develop solutions for renewable energy generation – mainly solar photovoltaic power – and storage for the planned complex.
The parties will also explore opportunities for other similar projects in the region, Mumbai-headquartered Essar said at the time.
A third major clean steel project in the kingdom has been announced by Turkish steelmaker Tosyali Holding, which will invest up to $5bn in the venture. Tosyali said in January that it intends to produce steel with the help of green energy sources and will increase its solar energy output 10-fold to 2,500MW, up from the 240MW it currently uses.
Fuat Tosyali, Tosyali’s chairman, said the increase in solar output will be facilitated by a $1.5bn investment, as well as through plans to buy a stake in a hydrogen energy company.
UAE makes strides
Clean steel production efforts in the UAE have been led by Emirates Steel Arkan, the country’s largest steel manufacturer. The company has partnered with Japan's Itochu to develop a low-carbon iron processing plant in Abu Dhabi that will be capable of processing high-grade Brazilian iron ore into reduced iron, which will be sent to Japan.
The proposed plant will be built in collaboration with Japan’s JFE Steel and is expected to produce about 2.5 million metric tonnes a year of reduced iron starting in 2027. CSN Mineracao, a Brazilian company in which Itochu maintains a stake, will supply the iron ore.
Emirates Steel and Abu Dhabi National Energy Company (Taqa) have also started the concept design for an electrolyser plant that they are jointly developing. Powered by renewable energy, the plant will have a hydrogen output capacity of 160MW, which will be used in the production of steel.
Abu Dhabi aims to establish a large-scale steel production hub with an overall capacity of 15 million t/y. This projected capacity will be in addition to Emirates Steel Arkan's existing production level of 3.5 million t/y, according to the firm's group chief projects officer, Hassan Shashaa.
Meanwhile, Dubai-headquartered Liberty Steel signed an MoU in December 2023 with Abu Dhabi’s AD Ports Group to invest in a green iron production facility in Khalifa Economic Zones Abu Dhabi.
Under the MoU, the two companies will explore the establishment of a green iron production facility and related port infrastructure and conveyor system at Khalifa Port in Abu Dhabi. The MoU is part of Liberty’s early-stage concept development to convert its magnetite ore into green iron in the UAE, using gas and transitioning to green hydrogen once it becomes available at scale in the next decade.
Green steel producers [in Oman] could benefit from cheap, locally available green hydrogen feedstock
Oman’s green steel plans
The largest green steel project in Oman is being developed by Vulcan Green Steel (VGS), the steel arm of Vulcan Green, which is owned by India’s Jindal Steel Group. VGS broke ground on the estimated $3bn project in December 2023.
The planned facility, covering 2 square kilometres in the Special Economic Zone at Duqm (Sezad), will have two production lines of 2.5 million t/y each, comprising DRI units, an electric arc furnace and a hot strip mill.
Set for completion by 2026, the planned facility will primarily utilise green hydrogen to produce 5 million t/y of green steel. This will make it the world’s largest renewable energy-based green steel manufacturing complex once it is commissioned.
Sezad could also host another large-scale green steel project if Japanese steel manufacturer Kobe Steel and Tokyo-based Mitsui & Company are able to achieve the final investment decision on a preliminary agreement they signed in April last year to develop a low-carbon iron metallics project.
The two Japanese firms agreed to conduct a detailed business study in line with the goal of commencing low-carbon dioxide iron metallics production by 2027. The project is expected to produce 5 million t/y of DRI using a process called Midrex, where DRI is produced from iron ores through a natural gas or hydrogen-based shaft furnace.
Green steel producers in the sultanate could benefit from cheap, locally-available green hydrogen feedstock if the Amnah consortium – which won the first land block contract that Hydrogen Oman (Hydrom) auctioned last year – achieves the financial investment decision on its planned project by 2026.
The estimated $6bn-$7bn project will supply green hydrogen to domestic and overseas steel producers, Amnah project director Mark Geilenkirchen told MEED last year.
The planned integrated facility is expected to have a capacity of 220,000 t/y of green hydrogen and will require up to 4.5GW of renewable energy capacity. Unlike other projects in the region that aim almost exclusively to export their green hydrogen derivative products such as ammonia, Amnah is considering converting or using green hydrogen to support sustainable steel production.
Exclusive from Meed
-
-
-
Bahrain and US sign nuclear energy agreement
17 July 2025
-
Kuwaiti firm wins $53m Duqm coastal road contract
17 July 2025
-
All of this is only 1% of what MEED.com has to offer
Subscribe now and unlock all the 153,671 articles on MEED.com
- All the latest news, data, and market intelligence across MENA at your fingerprints
- First-hand updates and inside information on projects, clients and competitors that matter to you
- 20 years' archive of information, data, and news for you to access at your convenience
- Strategize to succeed and minimise risks with timely analysis of current and future market trends
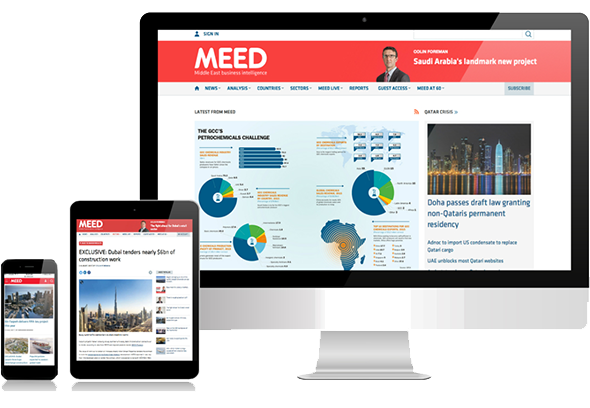
Related Articles
-
Riyadh Royal Commission awards metro Line 2 extension
18 July 2025
Register for MEED’s 14-day trial access
Saudi Arabia’s Royal Commission for Riyadh City (RCRC) has awarded an estimated $800m-$900m contract to build the next phase of the Riyadh Metro project, which is the Line 2 extension.
The contract was awarded to the Arriyadh New Mobility Consortium.
The Line 2 extension is 8.4 kilometres (km) long, of which 1.3km is elevated and 7.1km is underground. It includes five stations – two elevated and three underground.
It will run from where Line 2 currently ends at King Saud University (KSU) and then travel onwards to new stations at KSU Medical City, KSU West, Diriyah East, Diriyah Central, where it interchanges with the planned Line 7, and then finally to Diriyah South.
According to the consortium’s official website, the consortium members include Italy’s Webuild, India’s Larsen & Toubro, locally based Nesma & Partners, Japan’s Hitachi, Italy’s Ansaldo STS, the Canadian firm Bombardier, Spain’s Idom and WorleyParsons from Australia.
In 2013, the Arriyadh New Mobility Consortium secured Riyadh Metro’s Line 3 project for $5.21bn.
Line 3, also known as the Orange Line, stretches from east to west, from Jeddah Road to the Second Eastern Ring Road, covering a total distance of 41km.
Riyadh Metro
Riyadh Metro’s first phase features six lines with 84 stations.
The RCRC completed the phased rollout of the Riyadh Metro network when it started operating the Orange Line on 5 January.
In December last year, the RCRC started operating the Red Line and Green Line.
The Red Line, also known as Line 2, stretches 25.1km from the east of Riyadh to the west, via King Abdullah Road, connecting King Fahd Sports City and King Saud University. It has a total of 15 stations.
The Green Line, also known as Line 5, extends 13.3km from King Abdullah Road to the National Museum. With 12 stations, it serves several ministries and government agencies, including the Defence Ministry, the Finance Ministry and the Commerce Ministry, as well as other areas.
Earlier in December, the RCRC started operating the Blue Line (Line 1), Yellow Line (Line 4) and Purple Line (Line 6).
The Blue Line connects Olaya Street to Batha; the Yellow Line runs along King Khalid International Airport Road; while the Purple Line connects Abdul Rahman Bin Awf Road with Al-Sheikh Hassan Bin Hussain Road.
King Salman Bin Abdulaziz Al-Saud inaugurated the Riyadh Metro on 27 November last year.
The network spans 176km. Four of the stations have been designed by signature architects.
The metro is part of the Riyadh Public Transport Project, which encompasses metro and bus systems. The project aims to relieve traffic congestion.
The $23bn project was scheduled to open in 2018, but construction activity slowed due to disputes over prolongation and the disruption caused by the Covid-19 pandemic.
The RCRC awarded the main construction packages for the scheme on 28 July 2013.
In November 2022, the RCRC struck a deal with three contracting consortiums working on the Riyadh Metro scheme regarding the completion of the project’s remaining works.
The Fast consortium won lines 4, 5 and 6, reportedly valued at $7.82bn. The Bacs consortium was awarded lines 1 and 2 for $9.45bn, while Arriyadh New Mobility secured Line 3 for $5.21bn.
US firm Bechtel leads the Bacs consortium. Italian firm Ansaldo STS is the leader of the Arriyadh New Mobility group, and Spanish firm FCC Construccion heads the Fast consortium.
AtkinsRealis has delivered programme management and supervision services for the operations and maintenance of the Riyadh Metro scheme.
https://image.digitalinsightresearch.in/uploads/NewsArticle/14289337/main.jpg -
Firms submit bids for Maaden gold project water pipeline
17 July 2025
Saudi Arabian Mining Company (Maaden) has received proposals from local firms for a water pipeline network it plans to build as part of a larger project to develop a new gold mining and processing facility in the Al-Rjum region of the kingdom.
The Al-Rjum gold mining and processing facility, located in Medina province, is expected to be commissioned by the end of 2027. It will become the largest gold mining operation in Saudi Arabia when operational.
According to sources, the pipeline is to be developed using a build-own-operate-transfer (BOOT) model. The engineering, procurement and construction (EPC) works will have a duration of 38 months, followed by a 20-year operations and maintenance period.
Lamar Holding and Alkhorayef are understood to be the only bidders for the proposed Taif to Al-Rjum water pipeline, which forms package B of the Maaden gold mining project.
The two contractors submitted bids for the water pipeline project on 1 July, sources told MEED.
The main scope of work involves building a 150-kilometre pipeline that will supply treated sewage effluent water to the Al-Rjum gold mining facility.
ALSO READ: Saudi Arabia issues mining exploration licences
The Al-Rjum gold mining and processing facility will have an output capacity of 250,000 ounces of gold a year. The project will increase Maaden’s total gold production to 700,000 ounces a year by 2028, helping the company support Saudi Arabia’s overall goal of doubling gold production by 2030 and achieving a four-fold increase in output by 2040.
MEED recently reported that Maaden had received bids for a tender to develop accommodation facilities for over 4,500 of its workers at the upcoming Al-Rjum gold mining and processing facility.
Bids for the Al-Rjum worker accommodation tender, which is also under the BOOT model, were submitted in late June. The operations and maintenance period for this contract is 15 years.
ALSO READ: Saudi Arabia and Oman open up their minerals potential
https://image.digitalinsightresearch.in/uploads/NewsArticle/14284263/main3503.jpg -
Bahrain and US sign nuclear energy agreement
17 July 2025
Bahrain and the US have signed a cooperation agreement covering the field of peaceful nuclear energy.
The agreement aims to enhance collaboration in nuclear energy, recognising its vital role in sustainable development and energy security. It aligns with Bahrain's ambitious goal of achieving carbon neutrality by 2060 and contributes to global efforts to combat climate change.
As Bahrain explores alternative energy sources, senior officials have previously indicated to MEED that they are closely monitoring developments in small modular reactor (SMR) technology. This is particularly crucial for Bahrain, where limited land availability poses challenges for solar energy projects. Floating solar plants have been identified as a potential solution, but the exploration of nuclear energy and SMRs remains a priority for future energy diversification.
The agreement was signed during an official visit to the US by Prince Salman Bin Hamad Al-Khalifa, the crown prince and prime minister of Bahrain.
The agreement was formalised by Abdullatif Bin Rashid Al-Zayani, Bahrain’s minister of foreign affairs, and Marco Rubio, the US secretary of state.
Al-Zayani added that the agreement builds upon the Comprehensive Security Integration and Prosperity Agreement (C-SIPA) signed in 2023. The agreement aims to strengthen cooperation in defence, security, emerging technologies, trade and investment.
READ THE JULY 2025 MEED BUSINESS REVIEW – click here to view PDF
UAE and Turkiye expand business links; Renewed hope lies on the horizon for trouble-beset Levant region; Gulf real estate momentum continues even as concerns emerge
Distributed to senior decision-makers in the region and around the world, the July 2025 edition of MEED Business Review includes:
> AGENDA: UAE-Turkiye trade gains momentum> INTERVIEW 1: Building on UAE-Turkiye trade> INTERVIEW 2: Turkiye's Kalyon goes global> INTERVIEW 3: Strengthening UAE-Turkiye financial links> INTERVIEW 4: Turkish Airlines plans further growth> CURRENT AFFAIRS: Middle East tensions could reduce gas investments> GCC REAL ESTATE: Gulf real estate faces a more nuanced reality> PROJECTS MARKET: GCC projects market collapses> INTERVIEW 5: Hassan Allam eyes role in Saudi Arabia’s transformation> INTERVIEW 6: Aseer region seeks new investments for Saudi Arabia> LEADERSHIP: Nuclear power makes a global comeback> LEVANT MARKET FOCUS: Levant states wrestle regional pressures> GULF PROJECTS INDEX: Gulf projects index continues climb> CONTRACT AWARDS: Mena contract award activity remains subdued> ECONOMIC DATA: Data drives regional projects> OPINION: A farcical tragedy that no one can endTo see previous issues of MEED Business Review, please click herehttps://image.digitalinsightresearch.in/uploads/NewsArticle/14281751/main.jpeg -
Kuwaiti firm wins $53m Duqm coastal road contract
17 July 2025
Kuwaiti contractor Combined Group Contracting Company (CGCC) has won a RO20.6m ($53m) contract to construct coastal roads in Duqm.The scope of work covers the construction of roads with a total length of 14 kilometres, including a coastal road, a proposed service road, an extension to an existing service road, a resort street, four roundabouts, future extensions and proposed links.
The contract duration is two years from the start date of construction.
MEED reported in August 2023 that CGCC had emerged as the lowest bidder for the project.
GlobalData estimates that the construction industry in Oman will grow by 3.6% in real terms in 2025, supported by rising foreign direct investment (FDI) in the country, particularly in the manufacturing sector, as well as investment in the energy and transport sectors.
The infrastructure construction sector is estimated to grow by 5.7% in 2025, before recording an annual average growth of 5.2% between 2026 and 2029, supported by the government’s investment in upgrading road and airport infrastructure.
CGCC’s contract win in Oman comes shortly after a key contract win in the UAE, worth AED685m ($186m).
The scope of work under this contract encompasses the upgrade works on Emirates Road, from the Al-Badea intersection in Sharjah to the E55 intersection in Dubai.
The UAE’s Ministry of Energy & Infrastructure is the project client.
The contract duration is 25 months.
READ THE JULY 2025 MEED BUSINESS REVIEW – click here to view PDF
UAE and Turkiye expand business links; Renewed hope lies on the horizon for trouble-beset Levant region; Gulf real estate momentum continues even as concerns emerge
Distributed to senior decision-makers in the region and around the world, the July 2025 edition of MEED Business Review includes:
> AGENDA: UAE-Turkiye trade gains momentum> INTERVIEW 1: Building on UAE-Turkiye trade> INTERVIEW 2: Turkiye's Kalyon goes global> INTERVIEW 3: Strengthening UAE-Turkiye financial links> INTERVIEW 4: Turkish Airlines plans further growth> CURRENT AFFAIRS: Middle East tensions could reduce gas investments> GCC REAL ESTATE: Gulf real estate faces a more nuanced reality> PROJECTS MARKET: GCC projects market collapses> INTERVIEW 5: Hassan Allam eyes role in Saudi Arabia’s transformation> INTERVIEW 6: Aseer region seeks new investments for Saudi Arabia> LEADERSHIP: Nuclear power makes a global comeback> LEVANT MARKET FOCUS: Levant states wrestle regional pressures> GULF PROJECTS INDEX: Gulf projects index continues climb> CONTRACT AWARDS: Mena contract award activity remains subdued> ECONOMIC DATA: Data drives regional projects> OPINION: A farcical tragedy that no one can endTo see previous issues of MEED Business Review, please click herehttps://image.digitalinsightresearch.in/uploads/NewsArticle/14281451/main.gif -
Algeria awards $855m contract for gas production project
17 July 2025
Register for MEED’s 14-day trial access
Algeria’s national oil and gas company Sonatrach has awarded an $855m contract to China’s Jereh Group for a project to develop facilities at the Rhourde Nouss gas field.
Jereh Group said that its subsidiary Jereh Oil & Gas Engineering will build a natural gas booster station in the Rhourde Nouss gas field and upgrade and renovate related transmission pipelines.
The Yantai-based company cited a letter of award from Sonatrach and said that the contract will boost the company's footprint in North Africa’s oil and gas engineering service sector.
The Rhourde Nouss boosting project will centralise the boosting of natural gas produced by the gas field and the adjacent Gassi Touil gas field, to improve their production efficiency and natural gas processing capacity, the company said.
Sonatrach, the largest gas producing company in Africa and the largest state-owned enterprise in Algeria, will pay $629.1m and $226m for the construction of the project, Jereh said.
Jereh's growing footprint
Jereh has been expanding overseas in recent years and has won contracts with major Middle Eastern oil and gas clients, including Saudi Aramco, Abu Dhabi National Oil Company (Adnoc) and Kuwait Petroleum Corporation.
In June 2021, the company was awarded a contract for the design, procurement and construction of a gas debottlenecking project in Algeria.
The project was located in the Bir Rebaa Nord and Rhourde Ouled Djemma fields, which are located in the eastern Algerian desert, about 300 kilometres southeast of Hessi Messaoud.
The client on that project was Groupement Sonatrach Eni, a joint venture of Sonatrach and Italian energy company Eni.
READ THE JULY 2025 MEED BUSINESS REVIEW – click here to view PDF
UAE and Turkiye expand business links; Renewed hope lies on the horizon for trouble-beset Levant region; Gulf real estate momentum continues even as concerns emerge
Distributed to senior decision-makers in the region and around the world, the July 2025 edition of MEED Business Review includes:
> AGENDA: UAE-Turkiye trade gains momentum> INTERVIEW 1: Building on UAE-Turkiye trade> INTERVIEW 2: Turkiye's Kalyon goes global> INTERVIEW 3: Strengthening UAE-Turkiye financial links> INTERVIEW 4: Turkish Airlines plans further growth> CURRENT AFFAIRS: Middle East tensions could reduce gas investments> GCC REAL ESTATE: Gulf real estate faces a more nuanced reality> PROJECTS MARKET: GCC projects market collapses> INTERVIEW 5: Hassan Allam eyes role in Saudi Arabia’s transformation> INTERVIEW 6: Aseer region seeks new investments for Saudi Arabia> LEADERSHIP: Nuclear power makes a global comeback> LEVANT MARKET FOCUS: Levant states wrestle regional pressures> GULF PROJECTS INDEX: Gulf projects index continues climb> CONTRACT AWARDS: Mena contract award activity remains subdued> ECONOMIC DATA: Data drives regional projects> OPINION: A farcical tragedy that no one can endTo see previous issues of MEED Business Review, please click herehttps://image.digitalinsightresearch.in/uploads/NewsArticle/14278458/main.jpg