A case study in procurement
18 March 2025
Register for MEED’s 14-day trial access
While it may not be in the headlines as much as some of its more eye-catching official gigaproject counterparts, Roshn has already delivered thousands of residential units in Saudi Arabia as it seeks to fill the upscale and community living housing map.
Launched in 2020, the Roshn gigaproject is a component of the Vision 2030 plan to achieve 70% home ownership among Saudi nationals by 2030. Alongside the National Housing Company, it is the delivery vehicle for government-backed housing construction as Riyadh seeks to meet the shortfall in available stock.
Its first project was its Sedra community in the north of the capital. Currently on its fourth of eight delivery phases, the multibillion-dollar masterplanned development will comprise 30,000 homes over 20 million square metres (sq m) when completed.
Roshn’s second Riyadh community under construction is Warefa in the northeast of the capital. More compact than Sedra, it will have 2,300 units over an area of 1.4 square kilometres, with 150,000 sq m of green open space.
Three years after the launch of its first projects, Roshn announced Marafy, its first scheme in Jeddah and its largest mixed-use development to date. Designed to accommodate more than 130,000 residents, Marafy will be built around an 11-kilometre, 100-metre-wide canal, linking with Obhur Creek in the northern outskirts of the kingdom’s second city.
Already breaking ground, Marafy’s first core component is the Alarous residential community, which will offer 18,000 units over a 4 million sq m land area.
Elsewhere in the kingdom, Roshn’s other planned community projects include Almanar in Mecca, Alfulwa in Hofuf and Aldanah in Dhahran. Between them, these schemes total more than 50,000 units. It is expected that thousands of additional homes in other parts of the kingdom will be announced by the developer in the next two years.
Delivering such projects at many different locations is a complex exercise, requiring procurement strategies that not only encompass on-time and on-budget completion, but also ensure that local content is maximised while at the same time maintaining stringent quality standards.
Tasked with handling Roshn’s overall procurement strategy is Iain McBride, the gigaproject developer’s head of commercial.
It is expected that thousands of additional homes in other parts of the kingdom will be announced by the developer in the next two years
Like other gigaprojects in the kingdom, McBride and his procurement team have had to deal with the twin challenges of soaring cost inflation and maximising local content in materials and equipment.
The five official gigaprojects – Diriyah, Neom, the Red Sea Project, Qiddiya and Roshn – are free to employ their own procurement rules and processes, and each has taken a different approach to address its specific requirements. For example, Red Sea Global uses a construction management approach wherein it contracts directly with companies and suppliers that would normally work as subcontractors under the main contractors.
Similarly, Diriyah Company employs a strategy of bundling several smaller contract packages into a single large contract, as a means of consolidating work to ensure lower costs and maintain contractor interest.
Hear directly from the gigaproject owners at the biggest construction event – The Saudi Gigaprojects 2025 Summit, happening in Riyadh from 12-14 May 2025. Click here to know more
Demand signalling
The nature of Roshn’s mainly residential projects means that from the outset it knew it would need thousands of items with similar specifications, such as doors; glass panes; sanitaryware; and heating, ventilation and air-conditioning systems.
To secure this supply chain, early on the company identified local manufacturers of these products and reached long-term agreements with them for the delivery of required materials.
“Our first step was signing a lot of long-term partnership agreements through master purchase agreements where we could leverage preferential rates,” says McBride, speaking to MEED in late January.
“Ultimately, it's all about balance and risk – derisking the opportunities for the supply chain by telling them how many doors, for example, we're going to need each quarter for the next five to 10 years. It gives confidence to the manufacturers that they can start committing to.”
Roshn was the first of the gigaprojects to publicly signal its demand requirements. In 2021, it announced that it would require at least 5 million doors, 3.5 million air-conditioning units, 4.3 million windows, 80 million sq m of tiles and 6.5 million pieces of sanitaryware. These numbers have since changed, but they are indicative of the scale of the supply chain challenge.
Armed with the knowledge that Roshn is both supported by its parent, sovereign wealth vehicle the Public Investment Fund (PIF), and that it is a central element of Saudi Vision 2030, local manufacturers had the confidence to commit to investing in production capacity to meet its needs.
Significantly, most of these deals have been with manufacturers within the kingdom, thereby maximising the local content aspects. Just as importantly, Roshn has not had to make any fixed orders – so-called ‘take-or-pay agreements’ – with suppliers, such is the latter’s faith in the developer.
“For the time being, we’ve not had to make any firm commitments,” says McBride. “We did look at it at one point, but our approach has always been to keep it as simple as possible by listening to the supply chain and seeing what they need. When we were speaking to them, it wasn’t their number one driver; they weren’t screaming at us saying, ‘We need you to give us a firm order’.
“Now, many people think a take-or-pay agreement is essential – where you commit to ordering [a certain quantity] of materials over a period of months or years and, if you don’t, you have to pay a penalty, thereby adding risk and complexity for the developer.
“What we were able to agree instead was that we'll be open and transparent with [the suppliers about] what we need. We said to ourselves, ‘Let's get a good price that works, whether we buy directly from the supplier or whether we include that supplier within our tenders with major contractors’. And we’ve seen great success with that approach, with multiple companies.”
The localisation push is supported by the design process. Wherever possible, the designs for Roshn’s projects incorporate and specify equipment and materials that are known to be manufactured locally.
There have been instances where specific, specialised materials and products are not produced in the kingdom, or not in the quantities required, such as marble and certain architectural facades.
Where this is the case, Roshn is keen to explore how it can help to build in-kingdom capacity. The developer has initiatives through which it looks to co-invest in production facilities that come with high capital requirements.
As McBride explains, Roshn is only one part of the huge and rapidly accelerating Saudi projects market ecosystem, and in helping to increase capacity, it is also putting itself in a position to help other developers with their supply chain needs.
A case in point is Roshn’s contract with China Harbour Engineering Company, which was awarded the $2bn deal in 2023 to build villas at Sedra and Warefa.
Part of the contract requires the Chinese contractor to set up a precast manufacturing facility on site at Sedra. In this way, Roshn could not only ringfence the plant for its own needs, but when it no longer requires the output, other projects could benefit from its production capacity.
“The factory has a 15-year lifespan, so any additional capacity will be there for another 10 years after our requirements are met,” says McBride. “In Riyadh, we have Expo 2030, the new airport, the stadiums and many other projects that could draw on its output.”
There are some situations where even this is not enough, particularly when it comes to contracting expertise. One such case is Roshn’s mandate to develop a 45,000-seat stadium in the southwest of Riyadh as part of the kingdom’s Fifa World Cup 2034 plans. On such a complex, highly engineered project, Roshn has insisted that an international contractor teams up with a local company as a condition of tender participation.
This insistence is based on Roshn’s experience overseeing the construction of a football stadium in Dammam alongside co-developer, Saudi Aramco. The project, which is being built by a joint venture of Belgium’s Besix and the local Albawani, is proceeding at a rapid pace and progress has been relatively trouble-free.
McBride says: “If we have to go abroad, let’s go abroad. But make sure it’s done in a smart way and that we’re not just throwing money out of the kingdom.”
Early contractor involvement
On the issue of contracting, it is well known that the massive amount of work in Saudi Arabia is stretching contractors to the limit, pushing up prices and straining labour, engineering and equipment resources.
Roshn’s approach to this challenge has been to engage with contractors at the earliest possible stage of project planning, specifically at the design phase, through an early contractor involvement (ECI) procurement framework. In this way, the company is able to obtain contractor feedback during concept and design and subsequently lower construction risk by improving a project’s constructability.
“It's about signposting the demand by getting the contractor in early, where you can really influence the design, the buildability and the value-engineering opportunities,” says McBride. “Ideally, we bring them in as quickly as possible during the concept stages, when there's very little cost to changing things.
“The worst thing for a contractor is receiving a [request for proposal] cold. They have to … come back in four weeks and then be squeezed for a best price, whereas with ECI they can add value. They really appreciate that.”
When asked to quantify the cost benefits of such an approach, McBride is forthright: “It’s not even a case of doing the maths,” he says. “We have a great example of where it’s worked on our Aldanah project in Dammam. We selected the contract very early on and locked in the floor plans and facades that we wanted. We were then able to deliver a street of 10 show homes [that took] not much more than four months to design and construct.
“The saving, in terms of time, was massive; we probably halved the duration. I probably wouldn’t be exaggerating if I said it saved about a year.
“There are two ways you can follow your engineer,” he continues. “One: you can follow them early and make sure that the way you're looking to save costs is in areas that are not impacting the customer.
“Or two: the worst thing you can do is get to the end and you have a full structural design that could be over-engineered and you’re spending money in the wrong places.
“We don’t want to get to a point where we're trying to value-engineer by cutting things out that are important to customers,” McBride explains. “And that's what you avoid by having this early contractor involvement.”
The company is able to obtain contractor feedback during concept and design and subsequently lower construction risk by improving a project’s constructability
Unlike the other gigaprojects, Roshn has been in the favourable position of being able to raise some revenue by marketing and selling its properties off plan. While this has been beneficial from a development perspective, it has also meant that the developer must get its pricing and housing specifications right if it is to develop homes within an already-defined budget.
Having a contracting partner on board during the design and specification stage facilitates the conversation between the property sales team, which is informing on market requirements, and the builder, who can deliver within the designed cost and quality parameters.
This is in contrast to many real estate developments for which sales are completed before the construction estimates come in, potentially undermining the business case.
The step beyond ECI is for contractors and suppliers to partner with Roshn to inject equity into the projects by acting as co-developers. McBride points to several planned mid-rise towers at Marafy that could be a starting point for this.
Contractors financing projects or bringing in replacement equity has long been an ambition in the region, but builders have been reluctant to adopt this approach. Nonetheless, McBride is confident that it could happen, indicating that there has already been strong interest from the contracting community.
Cost inflation
Another major talking point in Saudi construction is the escalating costs caused by high inflation, logistical challenges and a tightening of contracting and skilled labour capacity.
In many cases, this has required the rescoping of projects, revisions to timelines and even the scrapping of elements. Neom is arguably the best example of this, as it has reprioritised The Line and is facing an estimated cost of $50bn for building each of its first three modules – far in excess of original estimates.
Roshn’s approach to the challenge is to be as open and transparent as possible with the contractor and supplier community. This has involved outlining a long-term pipeline of work that gives the supply chain confidence about its requirements, enabling them to fix in long-term pricing structures. In return, the developer expects prices to come in competitively.
“It’s no secret within the supply chain market that Roshn has quite aggressive price points,” says McBride, a former chartered surveyor who, prior to joining Roshn, worked as a quantity surveyor and cost-management director at consultants Faithful+Gould (now AtkinsRealis) and Rider Levett Bucknall.
“What we're trying to do is engage early, build trust with the contractors, let them see we’re a good client that's going to pay and have honest and fair contracting terms, and work together to try and solve issues post-contract.
“We don't mind if there's inflationary pressures because of commodity prices increasing. But what we're trying to avoid is inflationary prices through just the demand increasing.
“An innovative way that we've implemented this even on our lump-sum contracts – our traditional Redbook or older contracts – is that we have preferred supplier agreement clauses in them,” he adds.
“So, rather than a traditional bill of quantities (BoQ) that has a rate, a quantity, a total, within our rate section we have the material supply rate, the installation rate and then everything else, such as overhead profit. We protect the installation rate, so it's not a percentage of the material; it's a fixed SR100 a square metre to install, for example.
“One of the big frustrations for contractors is [that the supplier has] a material we think they're going to deliver. It's maybe not available, so they submit alternative materials. The client keeps rejecting it – it's not what they want – and it becomes a delay; it's painful.”
McBride gives the example of a pre-approved bathroom sink. Thanks to Roshn’s relationships with key long-term suppliers, the company is able to negotiate better rates for sanitaryware than would be available to a contractor on an ad hoc basis. If the developer’s rates for sinks are better than the BoQ, it splits the savings 50:50 with the contractor.
“The contractors are winning out of that exercise, we're winning out of it and, ultimately, the customers are winning out of it as well, because we’re passing on those savings,” says McBride.
Flexibility
The benefits to contractors and suppliers extend to payment terms. In today’s sellers’ market, vendors are effectively able to pick and choose the clients they want to work for. As a result, clients – including the gigaprojects – have had to introduce more flexible payment terms and develop market reputations for paying on time.
Roshn may lead the pack on this, with an average payment time from invoice to payment of just 13 days in 2024. A decade ago, this would have been unheard of, but it is now increasingly becoming the norm among the gigaprojects.
In addition, like its PIF peers, Roshn has done away with tender fees and tender bonds, viewing them as outdated means of enforcing vendor participation, especially given the tight liquidity and cashflow situation in the projects market in Saudi Arabia.
Will such flexibility ever extend to performance bonds? McBride is sceptical, pointing to the fact that Roshn’s strong relationship with local banks allows to it facilitate credit agreements between contractors and their lenders. Being a gigaproject developer supported by the PIF – and by tacit extension the state – also helps provide the underlining ease of mind for financers.
Nonetheless, Roshn also takes a proactive approach with advanced payments, enabling up to 20% of the total contract value at the initial stage of the project.
“We've been quite clever in how we do this,” says McBride. “We don't go and release 20% straight away. We’ll do 10% and then, when we’ve evidence that you’ve expended that 10% on mobilisation and site establishment, we’ll release the second 10% tranche.”
Subcontractors
One of the chief sticking points in the kingdom’s projects ecosystem in the past decade has been the capacity and capability of its subcontractors.
The payments crisis in 2017-20 forced many main and general contractors to reduce their permanent labour forces, plant and general resources. Wary of a repeat, most have retained their leaner structure and so have turned increasingly to subcontractors for their manpower and delivery requirements.
In theory, this makes sense, but in practice subcontractors in Saudi Arabia are themselves often overstretched in terms of both delivery capacity and labour availability. In turn, they frequently use their own subcontractors, which then also outsource, to the point that specific elements of a project may be completed by companies very far down the supply chain – with the quality issues that this implies.
Roshn’s solution is to ensure any subcontractor on site goes through a vetting process encompassing quality and financial checks, thereby ensuring it has full visibility on every company on site.
Increasingly, Roshn is dealing with suppliers directly, under supply-install contracts. This can create interfacing issues with the main contractors, however, which are ultimately responsible for the project’s delivery.
“We have to be quite careful on that,” McBride says. “We have to go through all the checks and balances during the prequalification process because if we are going to give a subcontractor to a contractor that we're saying is pre-vetted by Roshn, we could be opening the door to lots of claims from the main contractor against us. So, vetting for us is absolutely crucial.”
Roshn is also working with smaller suppliers and subcontractors to help them evolve and grow, so that they can start taking on smaller main contractor roles themselves.
“Not every construction package we award is in the billions of riyals,” says McBride. “Our thinking is to let the big tier-one contractors focus on the multibillion-riyal deals while we encourage the smaller ones to grow as part of our supplier development programme.”
To achieve this, the developer holds events and bootcamps with its vendors to discuss best practices on subjects including health and safety, variation procedures and how to submit good tender returns.
Roshn is also working with smaller suppliers and subcontractors to help them evolve and grow
Building information modelling
Vendor education also extends to the use of building information modelling (BIM) and other construction technologies.
BIM is mandatory on Roshn’s projects, as it is on the other gigaprojects. While use of the technology is standard across almost all main contractors in the region, its take-up among smaller companies in the supply chain has been slower, with firms pointing to the cost of its adoption and integration as a barrier, as well as the fact that some clients, particularly government ones, view it as providing limited benefit.
Roshn’s task in this area is made difficult because its projects are less complex from an engineering and construction perspective.
“We’re building villas; it’s completely different to building stadiums or airports,” McBride says. “Can these contractors build from [two-dimensional] drawings? Yes, of course they can. You're not going to convince a smaller contractor that all of these benefits will make it easier to build because they know how to build. They've been doing it for decades.
“But the savings are in making it easier to procure, savings in the repeatability, and in the change control. If you upskill yourself on a Roshn project, you are building your capability, which you can then [demonstrate] to other clients as proof you can go after bigger and more complex projects. It's something that the whole industry has to get behind.”
Indeed, there is much to learn from Roshn’s approach to delivering its infrastructure and building plans. While the comparatively straightforward nature of its projects means that its procurement strategies may not be suited to those gigaprojects with more iconic designs, for many other developers it is a case study in efficient processes that have proven effective in delivering work on time and to budget.
This is just as well given that Roshn is set to embark on the next stage of its journey, with its focus on the more complex Marafy city development in Jeddah and Roshn Stadium in Riyadh. However, the evidence suggests that from a procurement strategy perspective, it is well-positioned to also make this a success.
Exclusive from Meed
-
-
Firms bag $850m Qatar substation contracts
8 May 2025
-
-
Data centres churn investments
8 May 2025
-
Diriyah floats museum tender
8 May 2025
All of this is only 1% of what MEED.com has to offer
Subscribe now and unlock all the 153,671 articles on MEED.com
- All the latest news, data, and market intelligence across MENA at your fingerprints
- First-hand updates and inside information on projects, clients and competitors that matter to you
- 20 years' archive of information, data, and news for you to access at your convenience
- Strategize to succeed and minimise risks with timely analysis of current and future market trends
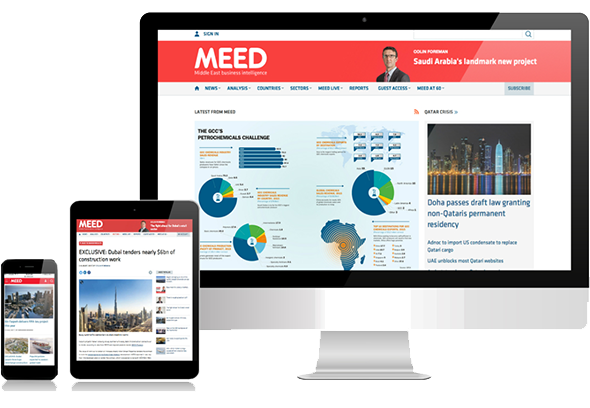
Related Articles
-
Abu Dhabi hopes bigger is better with Disney theme park
8 May 2025
Commentary
Colin Foreman
EditorEver since Aldar Properties first launched the Yas Island project with its Yas Marina Circuit for the Abu Dhabi Grand Prix in 2006, Abu Dhabi has been steadily adding theme parks to the island’s roster of attractions. First, there was the Ferrari theme park, then came a water park, a Warner Bros theme park and, most recently, SeaWorld.
The theory with theme park development is bigger is better.
A destination needs a series of parks to create a critical mass to attract visitors who can stay and enjoy multiple parks in one visit. The example always cited is Florida, which is home to many of the world’s largest theme parks, including Disney World.
The theory gained particular traction in the region when Dubai Parks and Resorts opened. The company, which was public until it was acquired by Meraas in 2021, reported significant losses as it struggled to attract enough visitors.
Although it opened with Legoland, Legoland Waterpark, Motiongate and Bollywood theme parks, insiders said that the problem with the development was that it did not have enough attractions to turn it into a successful theme park destination.
The financial performance of theme parks on Yas Island has not been publicly disclosed. While it is accepted that they have been more successful than their counterparts in Dubai, some say that the island still does not have the critical mass required to establish itself as a global destination for theme park visitors.
Miral has developed a series of theme parks and other entertainment-related attractions on Yas Island
Enter Disney
Disney changes that. It is the largest brand in the theme park space and will be a major attraction, but with limited information released on the project so far, it is difficult to fully gauge how significant the project will be.
The official release said that the project will be developed and operated by Abu Dhabi developer Miral, adding that Disney’s in-house design and engineering unit, Walt Disney Imagineering, will lead creative design and operational oversight to provide a world-class experience. It did not give any details on the ownership of the project.
In Hong Kong, for example, a company, Hong Kong International Theme Parks, was established as a joint venture, with the Government of Hong Kong holding 57% and The Walt Disney Company holding 43%.
In Japan, the structure is different. The Tokyo Disney Resort is owned and operated by Oriental Land, and the company pays licences and royalties to The Walt Disney Company.
In interviews following the launch announcement, Miral CEO Mohamed Abdalla Al-Zaabi confirmed the arrangement will be like Tokyo.
Waterfront location
The official release for the Abu Dhabi launch also said that the project is on Yas Island, which only has limited areas of land to develop. The release also said that the land is waterfront, and imagery in the launch video shows the Abu Dhabi skyline in the background, suggesting the land is on the northern waterfront of Yas Island.
There is a substantial tract of undeveloped land on the north shore of the island, which measures about 13 square kilometres (sq km). This is larger than the 4 sq km site that Hong Kong Disneyland occupies, but much smaller than Disney World in Florida, which spans an area of 111 sq km – nearly five times the size of the whole of Yas Island and nearly double the size of Abu Dhabi Island.
The hope is that Yas Island will become a leading global theme park destination and attract large numbers of visitors wanting a holiday with multiple theme park visits
Exclusivity clause
Another area of interest will be whether Abu Dhabi has an exclusivity agreement with Disney for the region. No exclusivity was mentioned at the launch, but in Hong Kong, the issue became contentious when Disney announced plans to build a park shortly after Disneyland Hong Kong opened. Local politicians criticised the Hong Kong government for not including an exclusivity clause in its deal with Disney.
Tourism gateway
Like Hong Kong, Abu Dhabi is a smaller economy sitting next to a larger regional player. With Saudi Arabia’s ambitious Vision 2030 strategy and its existing roster of theme park developments at Qiddiya, which includes a Six Flags, a water park and a Dragon Ball Z theme park, developers in Riyadh would likely be keen to have a Disney theme park, too.
For now, with Disney on board in Abu Dhabi, the hope is that Yas Island will become a leading global theme park destination and attract large numbers of visitors wanting a holiday with multiple theme park visits.
The potential is certainly there. During the project launch, Disney highlighted that the UAE is located within a four-hour flight of one-third of the world’s population, making it a significant gateway for tourism. It is also home to the largest global airline hub in the world, with 120 million passengers travelling through Abu Dhabi and Dubai each year.
If that potential is realised, then the bigger is better theory will be proved right. If the park’s performance disappoints, then it will suggest the region is not such a great destination for theme parks after all.
https://image.digitalinsightresearch.in/uploads/NewsArticle/13840555/main.gif -
Firms bag $850m Qatar substation contracts
8 May 2025
Four local and international firms have won contracts for the construction of seven high-voltage substations in Qatar.
State-backed Qatar General Electricity & Water Corporation (Kahramaa) signed the contracts, which have a total combined value of approximately QR3.1bn ($850m), with the following firms:
- Elsewedy Cables Qatar Company (local/Egypt)
- Voltage Engineering (local)
- Best/Betas Consortium (Turkey)
- Taihan Cable & Solution (South Korea)
Kahramaa said the projects aim to “meet electrical network demand in light of the country's fast-growing …urban development”.
The contracts include the provision and installation of underground cables and overhead lines extending around 212 kilometres to connect these substations.
Qatari companies won the largest share, equivalent to 58.4% or QR1.8bn, of the total contract value.
This reflects “our great confidence in the capabilities of the local private sector and its pivotal role in achieving our development vision and achieving Qatar National Vision 2030”, said Kahramaa president Abdulla Bin Ali Al-Theyab.
Qatar Minister of State for Energy Affairs, Saad Sherida Al-Kaabi, and senior executives from Kahramaa and the contracting firms signed the deals at a ceremony held in Doha.
Al-Kaabi said the projects will help “ensure our networks' continued and sustainable ability to accommodate the unprecedented growth of the power sector and meet the increasing electricity demand”.
Kahramaa said the contractors will undertake the construction of electrical substations and the connection of cables and overhead lines, as well as the development of some existing substations to increase their capacity.
Qatar has been ramping up its power generation capacity in recent years.
Qatar's Emir, Sheikh Tamim Bin Hamad Al-Thani, inaugurated the Ras Laffan and Mesaieed solar photovoltaic (PV) power plants on 28 April.
The two plants have a combined capacity of 875MW and will more than double Qatar’s solar energy production to 1,675MW.
In February, Qatar Electricity & Water Company (QEWC) and Kahramaa signed a power-purchase agreement for a 511MW peak electricity generation plant at Ras Abu Fontas, which will have a total cost of approximately QR1.6bn. The peak power plant is scheduled to become operational by January 2027.
A consortium led by South Korea's Doosan Enerbility, and that includes Beijing-headquartered PowerChina, will undertake the Ras Abu Fontas peak power plant's engineering, procurement and construction contract, with Germany's Siemens Energy supplying the plant's gas turbines.
Photo credit: Kahramaa
https://image.digitalinsightresearch.in/uploads/NewsArticle/13838850/main.jpg -
OQ to take interest in Oman renewable projects
8 May 2025
OQ Alternative Energy (OQAE), part of Oman’s state-backed energy group OQ, will be taking shares in Oman’s renewable energy independent power projects (IPP), starting with the Ibri 3 solar scheme.
“The direction seems to be for OQ Alternative Energy to own up to 25% shares in the upcoming solar and wind IPP projects in the sultanate,” says a source familiar with the plans.
Before this development, private developers and investors owned the total shares in such projects, similar to the existing structure in Saudi Arabia.
With this policy change, Oman will now be more closely aligned with the existing project structure in the UAE, where either Abu Dhabi National Energy Company (Taqa), Abu Dhabi Future Energy Company (Masdar) or the state utility, Dubai Electricity & Water Authority (Dewa), owns stakes in these projects.
However, OQAE’s planned 25% ownership share will be slightly lower than the typical 40% to 60% shares that Taqa, Masdar or Dewa owns in the UAE’s renewable energy IPP projects.
Currently, OQAE owns a 51% share in three renewable energy projects being developed in partnership with France’s TotalEnergies for the state-backed firm, Petroleum Development Oman (PDO).
The Riyah-1 and Riyah-2 wind power plants will be located in the Amin and West Nimr fields in southern Oman, while the North Solar project will be situated in northern Oman.
Each plant will have a capacity of 100MW, Total Energies announced in December.
PDO will purchase the electricity from the plants through long-term power-purchase agreements with the developer team, whose 49% shares are owned by TotalEnergies.
OQAE is also part of Hyport Coordination Company, a consortium comprising Belgium’s Deme Concessions and BP Oman. The consortium plans to develop a green hydrogen project in Duqm that can produce more than 50 tonnes a year of green hydrogen in its first phase by 2029.
https://image.digitalinsightresearch.in/uploads/NewsArticle/13838800/main.jpg -
Data centres churn investments
8 May 2025
Global investment firm KKR appointed retired US Army general and former Central Intelligence Agency director David Petraeus as chairman of its Middle East operations in mid-April.
The move is indicative of the region’s importance as a destination for the firm’s future investments, and capitalises on the strength of the relationships Petraeus has forged with Gulf country leaders during his years as a top US military strategist.
KKR’s most recent commitment in the region entails acquiring a stake in UAE-based Gulf Data Hub (GDH), which operates seven data centres in the UAE and Saudi Arabia. The UAE firm plans to build additional data centre facilities in Kuwait, Qatar, Bahrain and Oman, and KKR has committed to support its $5bn expansion plan.
“[Petraeus' appointment] is a good move on their part. It reinforces the region’s growing status and importance as a data centre investment destination, due to a significant interest in artificial intelligence (AI) deployments,” says a senior executive with an international data centre operator.
KKR’s prior investments in the region include a partnership with Abu Dhabi National Oil Company (Adnoc) in 2019 to create Adnoc Oil Pipelines, and acquiring a portfolio of commercial aircraft from Abu Dhabi’s Etihad Airways in 2020.
The private equity firm’s investment in GDH, however, shows only part of the picture as far as the rapidly evolving data centre investment landscape is concerned.
In March, Abu Dhabi-based critical infrastructure-focused sovereign investor ADQ and US-headquartered power developer Energy Capital Partners agreed to establish a 50:50 partnership to build new power generation and energy infrastructure that will serve the long-term needs of data centres and industrial clusters in the US and selected other international markets.
The two firms plan to make total capital investments of more than $25bn across 25GW-worth of projects. The combined initial capital contribution from the partners is expected to amount to $5bn.
That announcement came a day after UAE National Security Adviser and Deputy Ruler of Abu Dhabi, Sheikh Tahnoon Bin Zayed Al-Nahyan, met with US President Donald Trump at the White House. During the meeting, the UAE is understood to have committed to a 10-year, $1.4tn investment framework for the US.
Tech funds
In the past 24 months, Abu Dhabi and Riyadh in particular have set up funds, sometimes in partnership with global firms, to invest in AI and data centre infrastructure, both domestically and abroad.
Abu Dhabi’s MGX aims to build $100bn in assets under management within a few years, along with US-headquartered and Blackrock-backed Global Infrastructure Partners and Microsoft, the fund's key partners. It is part of the US’ Stargate consortium, which aims to mobilise up to $500bn to build AI infrastructure in the US over the next four years.
In Riyadh, a $100bn AI initiative known as Project Transcendence is expected to invest in data centres, technology startups and other related infrastructure for the development of AI.
US-based Silver Lake announced in March 2025 that, together with MGX, it has become a minority shareholder in state-backed, Abu Dhabi-based Khazna Data Centres, one of the region’s largest data centre operators.
In 2023, Saudi sovereign wealth vehicle the Public Investment Fund (PIF) partnered with US-based DigitalBridge to develop data centres in Saudi Arabia and across the GCC states.
In early 2025, Saudi Arabia-based DataVolt – which is owned by Vision Invest, a major shareholder in Saudi utility developer Acwa Power and a public-private partnership advocate – signed a preliminary agreement to build a data centre in Neom, Saudi Arabia. The $5bn facility, with an initial phase of 300MW, is the first of many such schemes that DataVolt is planning.
Not to be outdone, the founder of Dubai-based private real estate developer Damac pledged to invest $20bn in data centre projects in several US cities earlier this year.
And there is more to the growing – if outsized – number of bidirectional data centre-focused investment flows than meets the eye.
Given the global AI race and mounting competition, investment decisions regarding data centres are moving from a simple, commercial focus to account for complex geopolitical considerations, according to Jessica Obeid, a partner at Dubai-headquartered New Energy Consult.
“As the US weaponises its technological advancements, decisions to invest in US-based data centres hedge against the risks of US export controls, positioning developers in proximity to suppliers, ensuring reliable access to components.
“Yet, this access could become costlier, driven by trade tariff wars, heightened regulations and limited access to grid infrastructure,” Obeid says.
She adds that the GCC is quickly positioning itself as a global digital hub, driven by cost-competitive energy, advanced infrastructure and strong government backing.
“Proximity to reliable power supply at an affordable cost, and speed in licensing processes and grid connections, are increasingly becoming strategic factors in data centre deployment – and the GCC offers that.”
Powering AI strategies
Almost all of the GCC states have formulated AI strategies that aim to improve operational efficiencies, create jobs and support their energy transition and net-zero initiatives.
As a result, analysts expect the region to register double-digit annual growth in data centre construction activities in the next few years.
In a recent update, global consultancy PwC projected that the Middle East data centre capacity could triple from 1GW in 2025 to 3.3GW in five years’ time.
According to data from regional projects tracker MEED Projects, as of April, an estimated $12bn-worth of data centre construction projects are in the planning stage, in addition to over $820m under bid and $7bn under construction.
Li-Chen Sim, assistant professor of civil security at Abu Dhabi’s Khalifa University, says that AI investments are, on the one hand, “all part of a carefully conceived strategy to … diversify out of a hydrocarbons-driven economy, to create new revenue streams from overseas data centres, build new growth sectors, support business requirements and offer more knowledge-based jobs as opposed to traditional manufacturing from domestic investments”.
On the other hand, AI investments also aim to future-proof the hydrocarbons sector, which Sim expects will continue to be a significant driver of growth, revenue and exports, even as the use of renewable power grows.
However, the ability of Gulf states to execute their plans for leveraging AI to diversify economies and create jobs –and specifically to address youth unemployment – depends on two factors, according to Obeid.
The first factor is the ability of countries to advance their AI goals from infrastructure to capital and partnerships. The second involves the speed with which they can build up adequate human capital and a skilled workforce.
“We will have to see how governments align their educational curricula with the AI policies and electricity infrastructure development,” she says.
Ecosystem investment
AI and data centre investments go beyond the facilities that house thousands of advanced graphics processing units, miles of cables and many cooling systems. To run and execute applications – particularly AI inferencing tasks – data centre facilities require a substantial amount of energy.
Moreover, data centres in the Middle East and North Africa region face elevated environmental risks due to the high ambient temperatures, which increase energy demand for cooling, as well as water requirements.
This presents both a challenge and an opportunity, according to Obeid. "The GCC has an opportunity to advance innovation in energy and cooling technologies. Liquid cooling is necessary for AI workloads, and small modular reactors will become central in these data centres.”
In January, Abu Dhabi’s Emirates Water & Electricity Company (Ewec) appeared to show the way with a plan to build a round-the-clock solar photovoltaic (PV) plant combined with a battery energy storage system (bess) facility.
The 5.2GW solar PV and 19 gigawatt-hour bess plant is expected to deliver renewable power as baseload, and UAE President Sheikh Mohamed Bin Zayed Bin Sultan Al-Nahyan has said that the project will help power advancements in AI and emerging technologies, and support the delivery of the UAE National AI Strategy 2031 and 2050 Net Zero initiative.
Sim agrees that renewables combined with battery storage is part of the answer when it comes to building sustainable data centres. “Globally, data centres consume about 1% of electricity, and this figure – together with carbon emissions by data centres – is expected to grow significantly.”
He notes that Goldman Sachs Research forecasts that global power demand from data centres will increase 50% by 2027, and 165% by the end of the decade, compared to 2023.
“The other part of the puzzle with regard to sustainability is water consumption by data centres, particularly those in the Gulf, where high temperatures necessitate even more cooling measures.
“Singapore, for instance, has pioneered integrated water systems that recycle treated wastewater for reuse – and this circular water model could be an option for data centres in the Gulf, instead of using expensive desalinated water,” says Sim.
As things stand, the GCC can play a key role in the advancement of these and other technologies, along with efficiency measures and the optimisation of server utilisation through AI applications such as digital twins, says Obeid.
This is just as well, since the region appears to be on the cusp of a boom in inbound and outbound investments that will build data centre capacity abroad and closer to home.
“We are at a pivotal moment for innovation, where the intersection of digital advancements and energy innovation could position the GCC as a global leader, shaping the future of sustainable digital infrastructure,” concludes Obeid.
https://image.digitalinsightresearch.in/uploads/NewsArticle/13732105/main5907.jpg -
Diriyah floats museum tender
8 May 2025
Saudi gigaproject developer Diriyah Company has tendered a contract to build the new iconic museum in the DG2 area of the Diriyah project in Riyadh.
MEED understands that the tender was issued in April, with the bid submission deadline in June.
Diriyah completed the prequalification process for the project in February this year.
Diriyah Company is expected to award more multibillion-dollar contracts this year. In April, MEED exclusively reported that the client had awarded an estimated SR4bn ($1.1bn) contract for a utilities relocation package for the King Salman University (KSU) project located in the second phase of the Diriyah Gate development (DG2).
The contract was awarded to the joint venture of Beijing-headquartered China Railway Construction Corporation and China Railway Construction Group Central Plain Construction Company.
Last month, MEED also reported that the company had awarded an estimated SR5bn ($1.3bn) construction deal to build the Royal Diriyah Opera House.
The contract was awarded to a joint venture of local firm El-Seif Engineering & Contracting, Beijing-headquartered China State Construction Engineering Corporation and Qatari firm Midmac Contracting.
Tendering activity is also progressing on several other major schemes at Diriyah, including the King Khalid Road project, which passes through the development. The client received bids from firms in the second week of April for the main construction works on this project.
The client is also expected to finalise the contract award shortly for the Arena Block assets in the Boulevard Southwest section in the DG2 area.
Diriyah gigaproject
The Diriyah masterplan envisages the city as a cultural and lifestyle tourism destination. Located northwest of Riyadh’s city centre, it will cover 14 square kilometres and combine 300 years of history, culture and heritage with hospitality facilities.
The company awarded several significant contracts last year, including three contracts worth over SR21bn ($5.5bn). These included an estimated $2bn contract awarded to a joint venture of El-Seif Engineering & Contracting and China State to build the North Cultural District.
In late July, Diriyah also awarded a $2.1bn package to a joint venture of local contractor Albawani and Qatar’s Urbacon to construct assets in the Wadi Safar district of the gigaproject.
In December, MEED reported that Diriyah Company had awarded an estimated SR5.8bn ($1.5bn) contract to local firm Nesma & Partners for its Jabal Al-Qurain Avenue cultural district, located in the northern district of the Diriyah Gate project.
Once complete, Diriyah will have the capacity to accommodate 100,000 residents and visitors.
MEED’s April 2025 report on Saudi Arabia includes:
> GOVERNMENT: Riyadh takes the diplomatic initiative
> ECONOMY: Saudi Arabia’s non-oil economy forges onward
> BANKING: Saudi banks work to keep pace with credit expansion
> UPSTREAM: Saudi oil and gas spending to surpass 2024 level
> DOWNSTREAM: Aramco’s recalibrated chemical goals reflect realism
> POWER: Saudi power sector enters busiest year
> WATER: Saudi water contracts set another annual record
> CONSTRUCTION: Reprioritisation underpins Saudi construction
> TRANSPORT: Riyadh pushes ahead with infrastructure development
> DATABANK: Saudi Arabia’s growth trend heads uphttps://image.digitalinsightresearch.in/uploads/NewsArticle/13838747/main.jpg